Dies, integrated tooling and automation fit for your floor.
For 44 years, we’ve solved manufacturing challenges for thousands of programs with results that save you time, energy and money. We build solutions that work — often better than you could imagine.
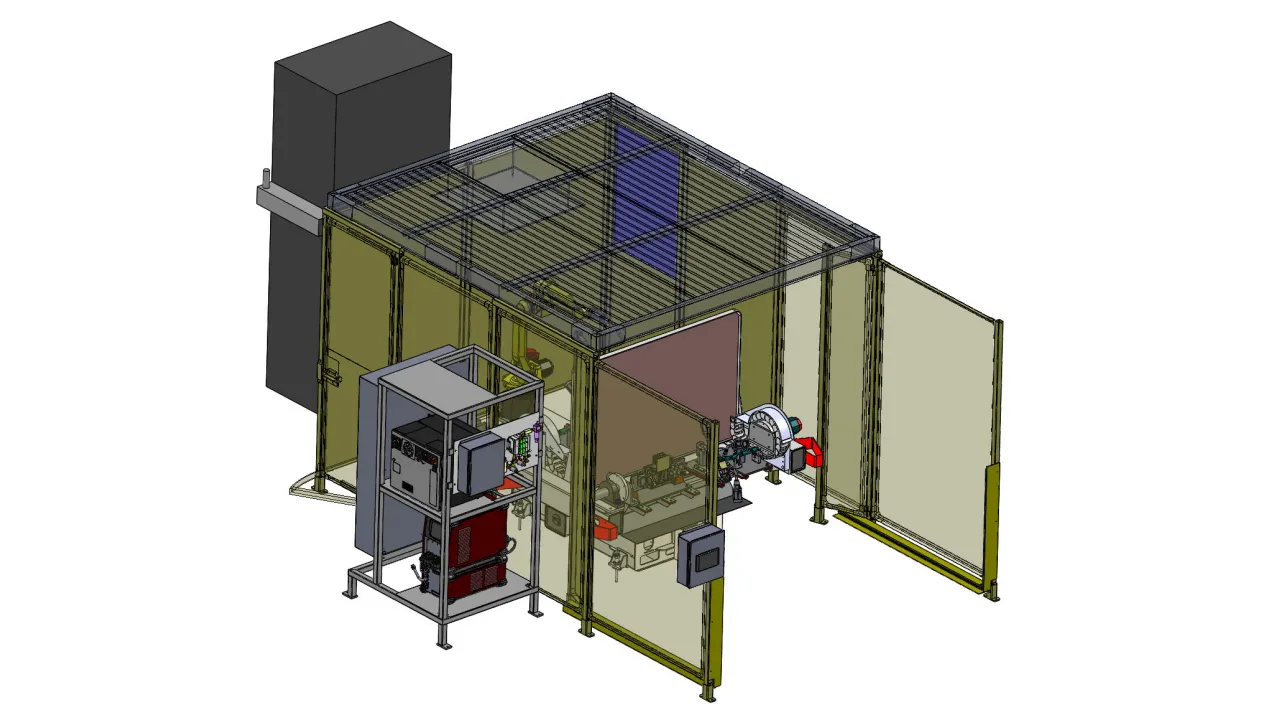
Custom Automation
From small assembly fixtures to lights-out cells and everything in between, we leverage our experience and cutting edge technology to create custom automation solutions that save customers money and speed up production.
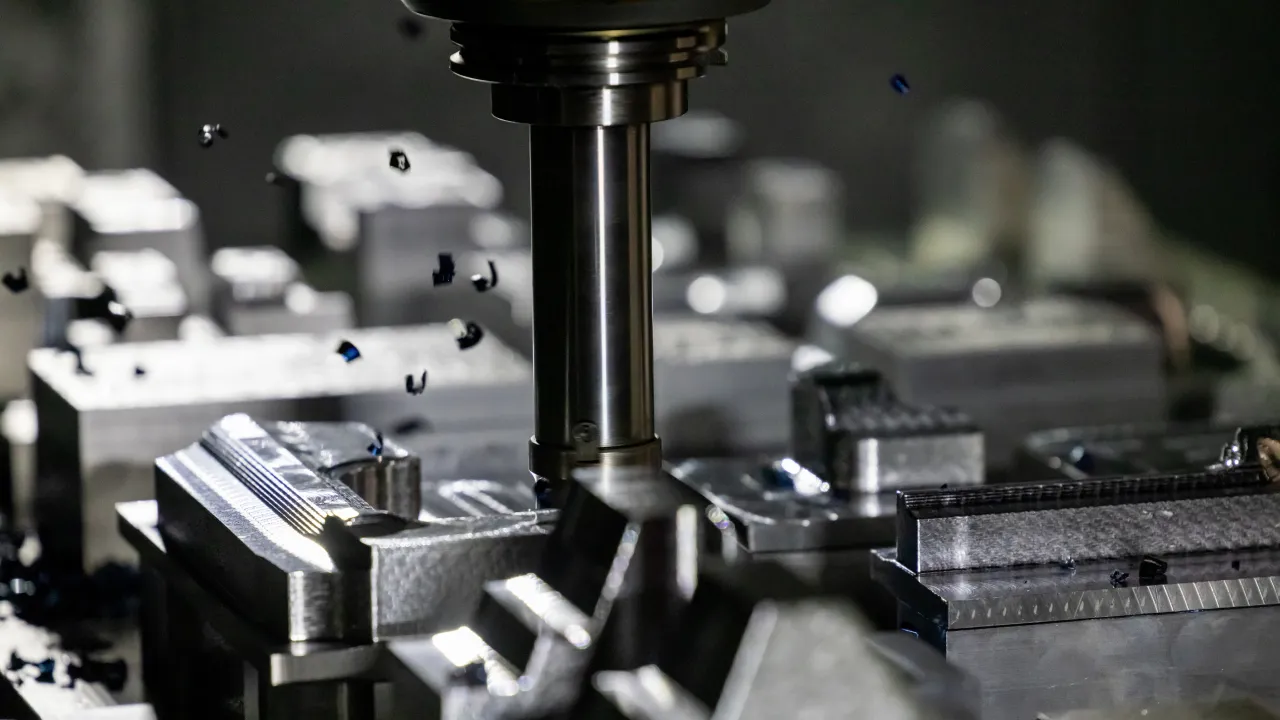
Metal Processing
We offer welding, machining, degate, bending, forming and trim dies for a wide range of metals. We integrate multiple technologies into metal processing equipment—to help deliver high-quality components that meet your specifications and exceed your expectations.
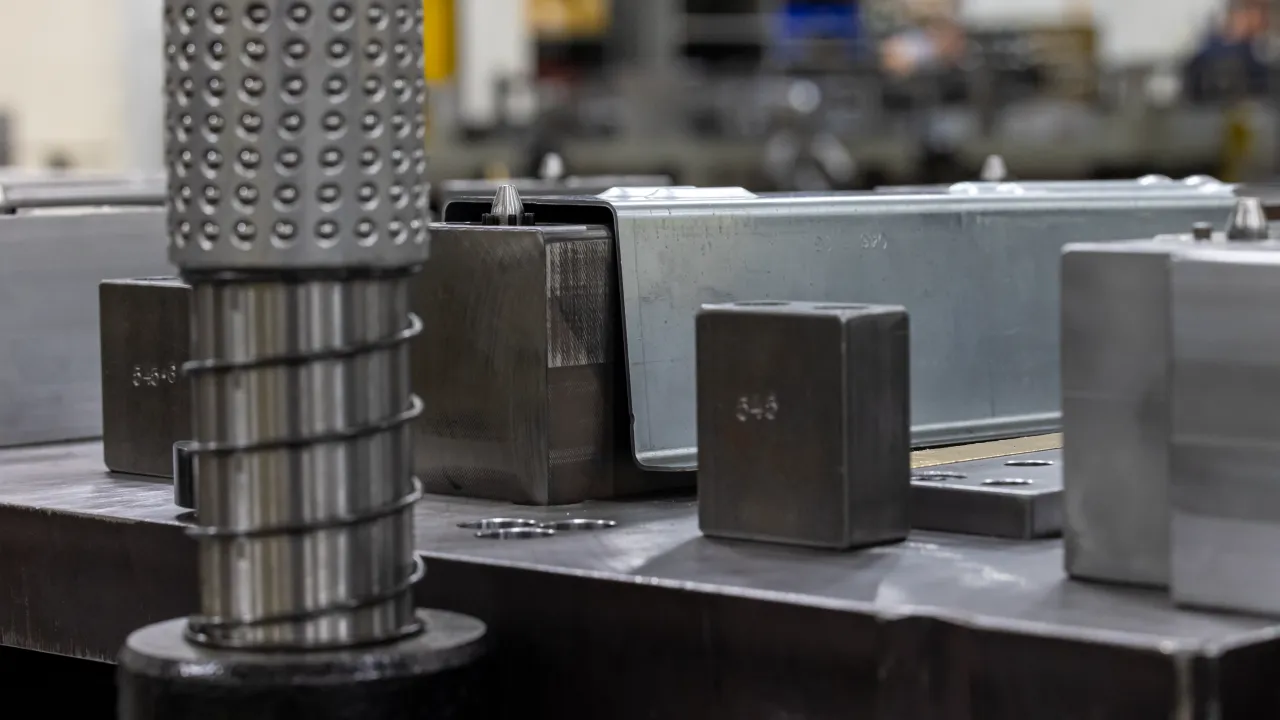
Stamping Dies
Our team can build dies for your simple and complex parts. We’re able to offer a range of progressive, transfer and line dies with consistent, high-quality results. Our approach to concepting and design saves you material costs and frustration for the life of your program.
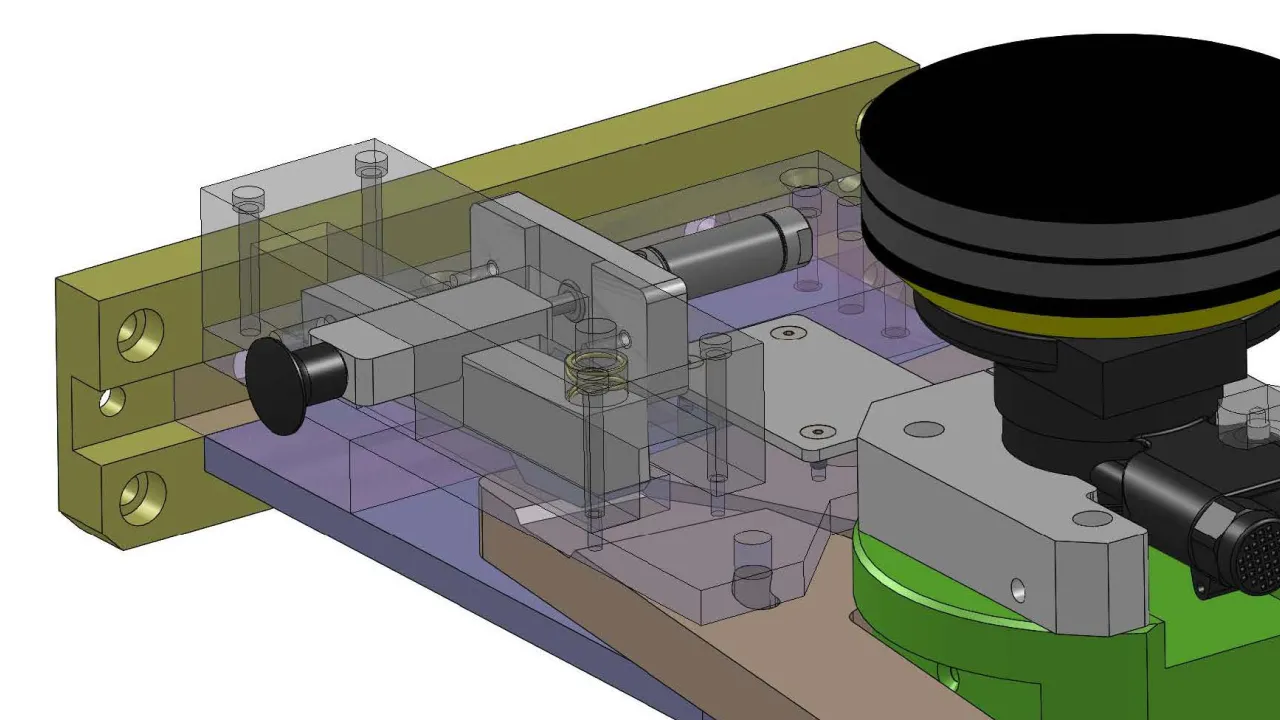
Carbon Fiber Processing
Processing Carbon Fiber takes as much art as science—our team uses both. Our teams have been able to combine the speed and accuracy of robotic tooling with the finesse and adjustability of sanding tools to eliminate extraordinary scrap and deliver precise results.
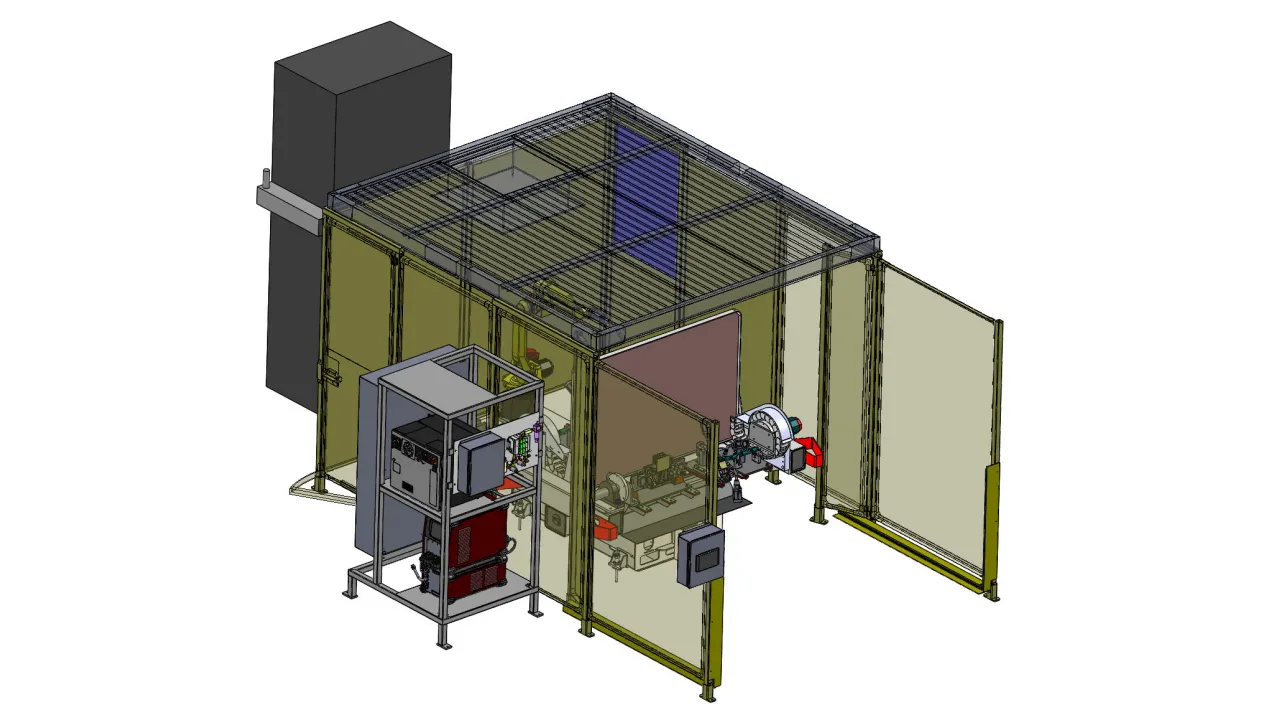
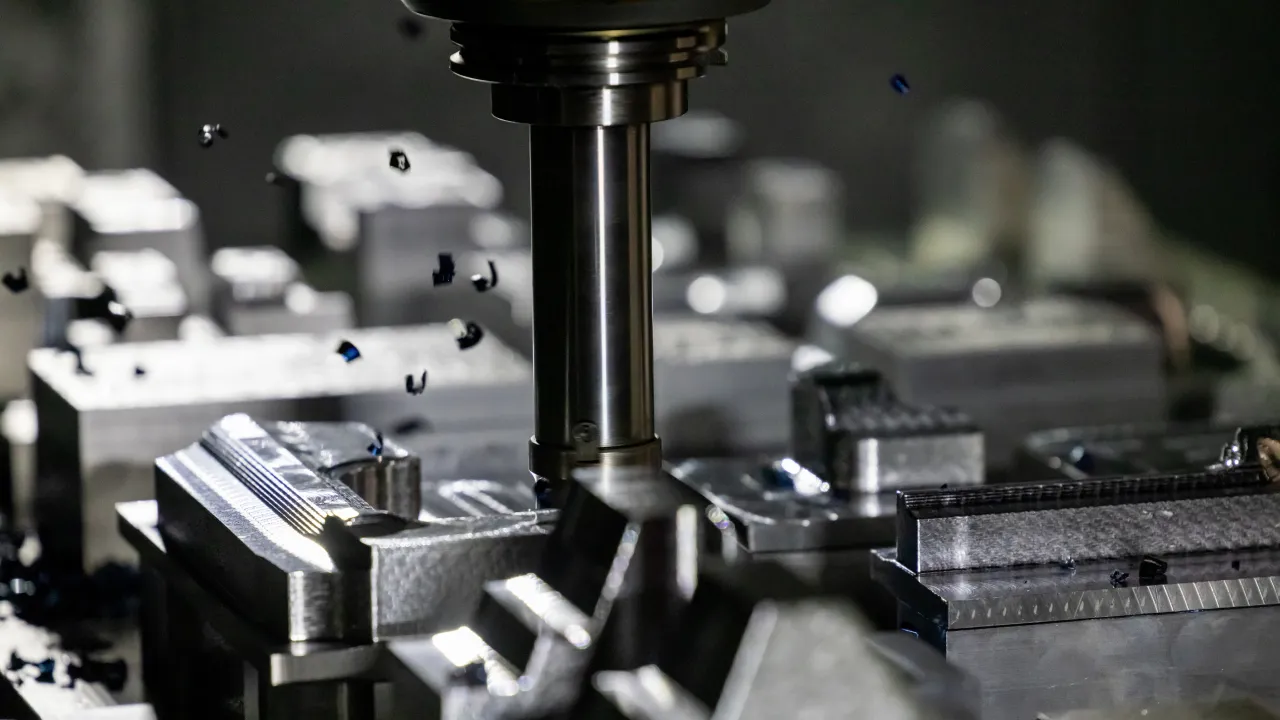
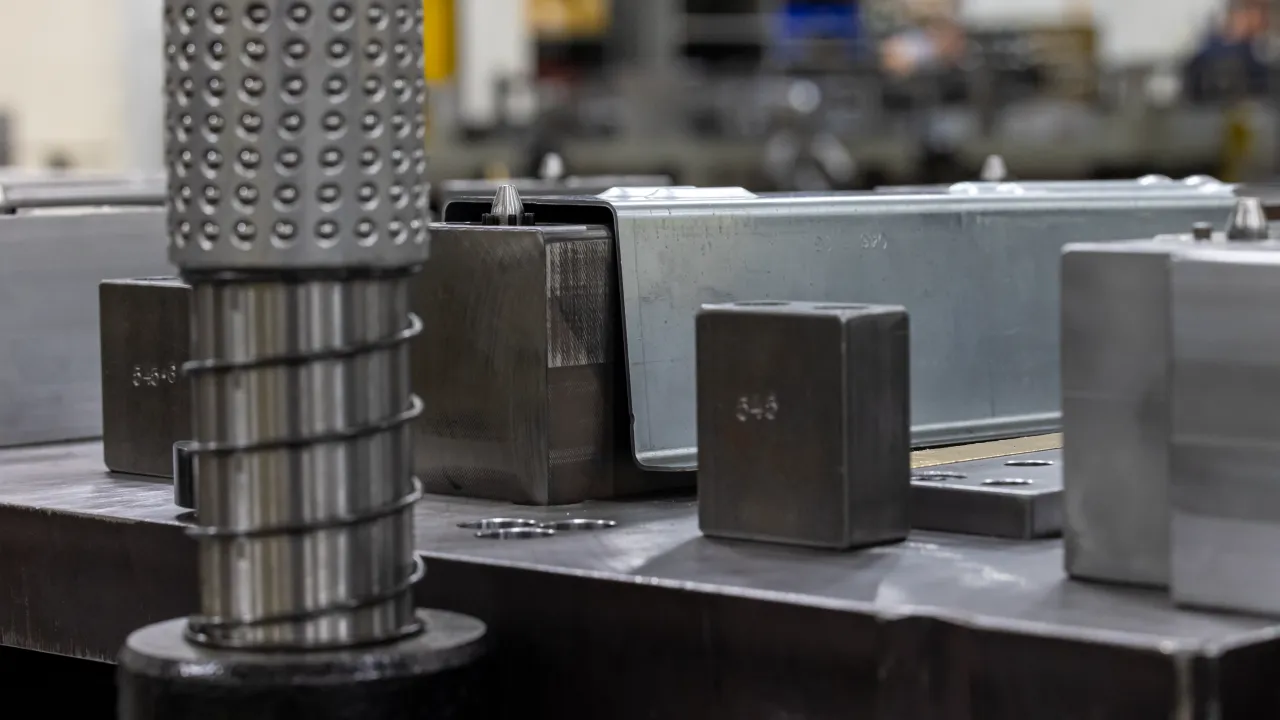
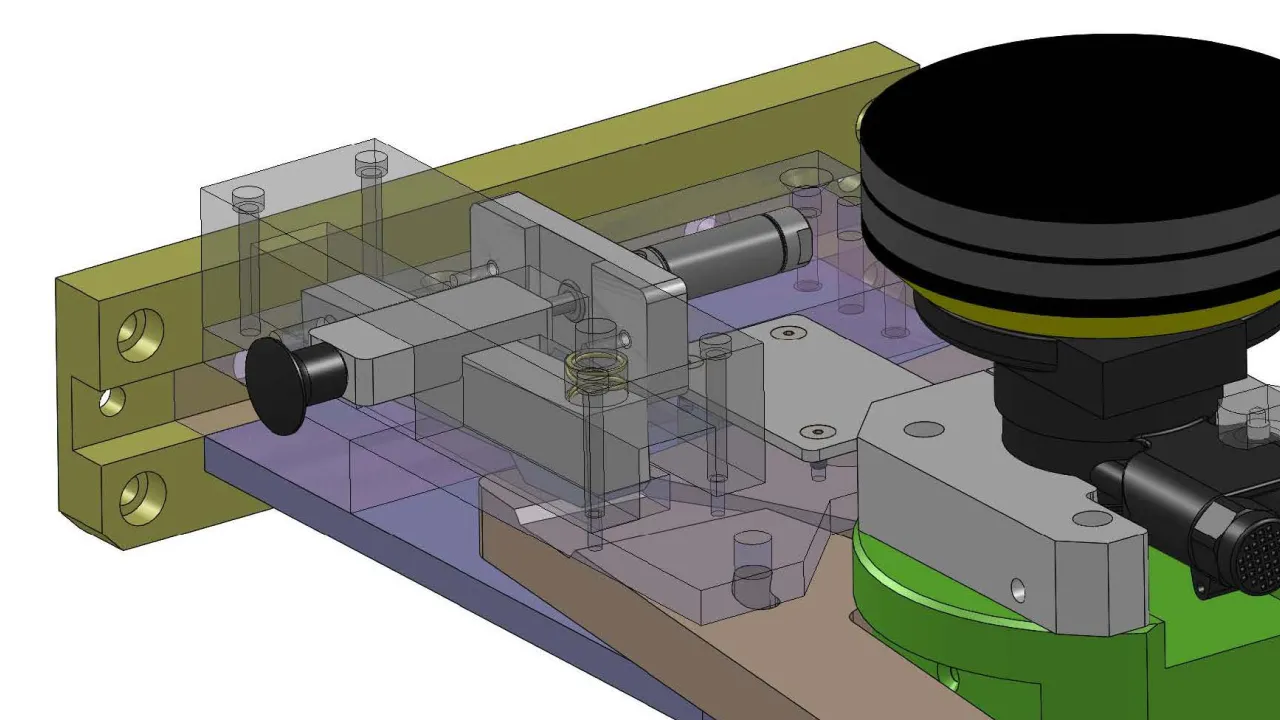
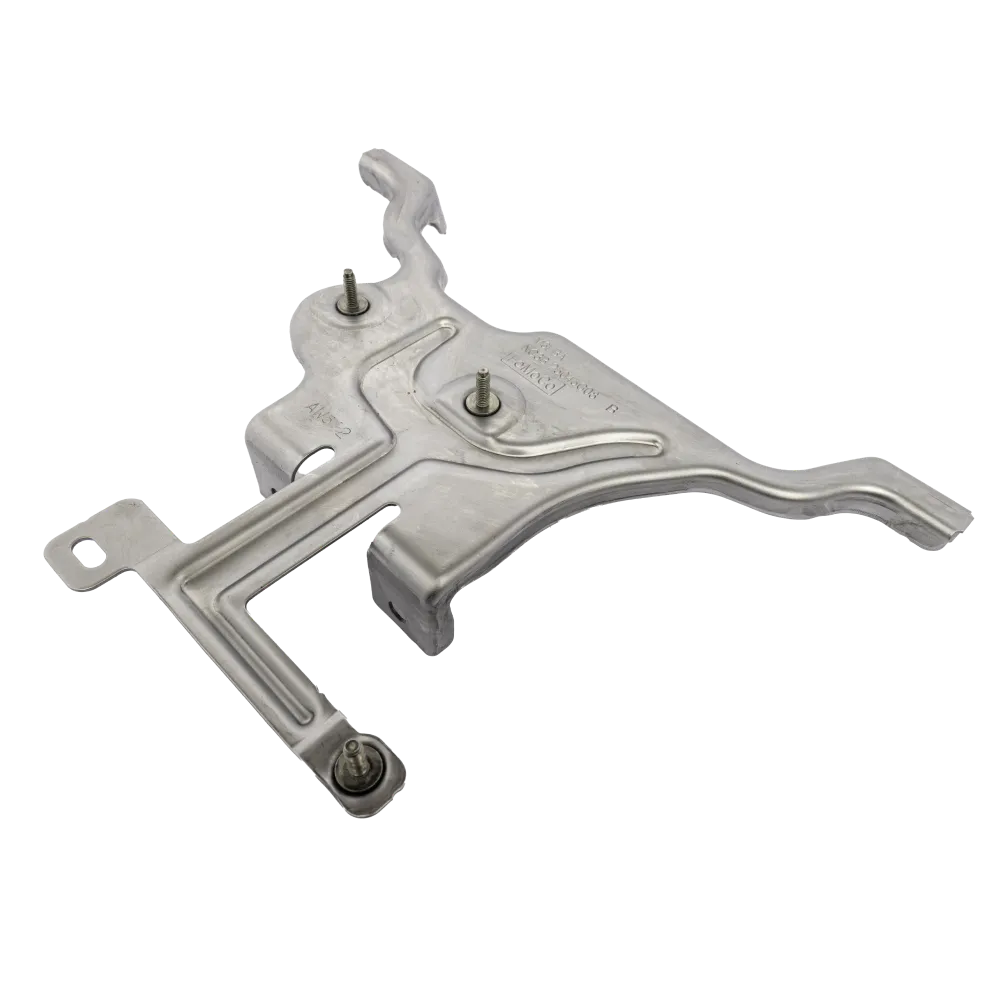
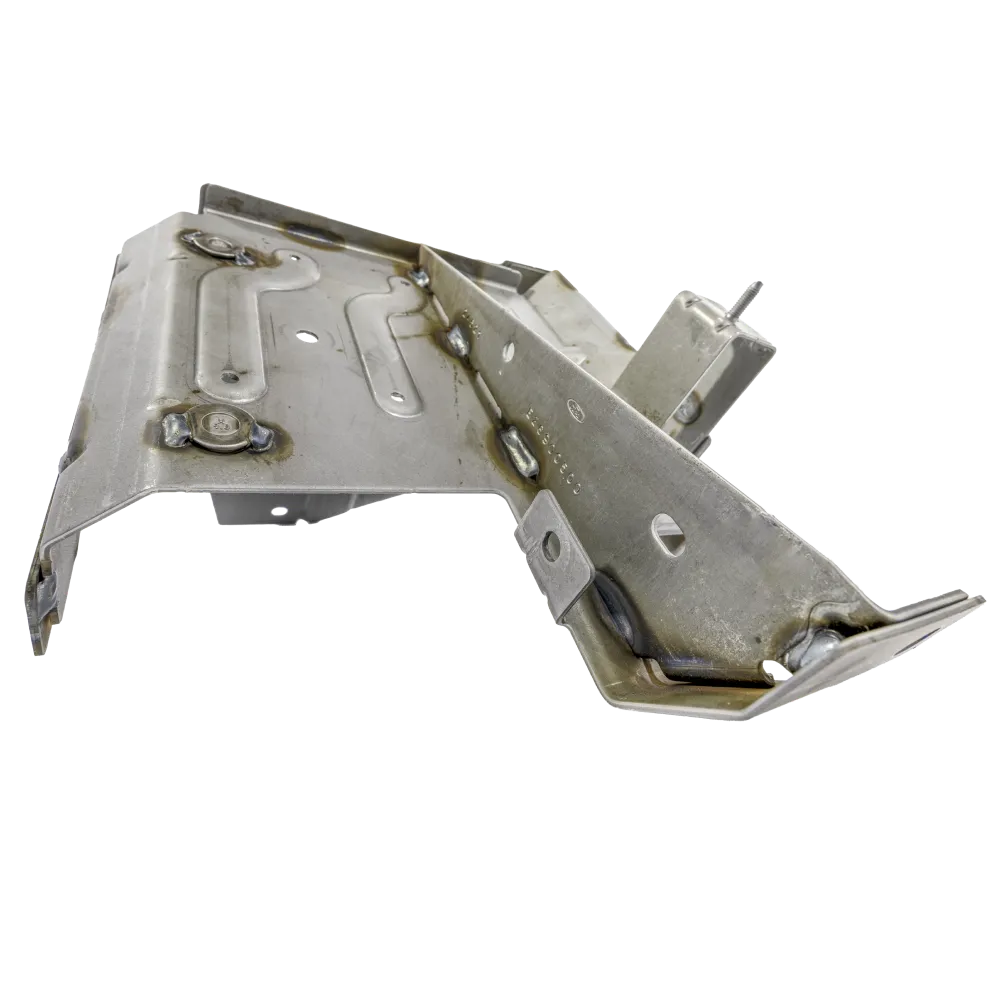
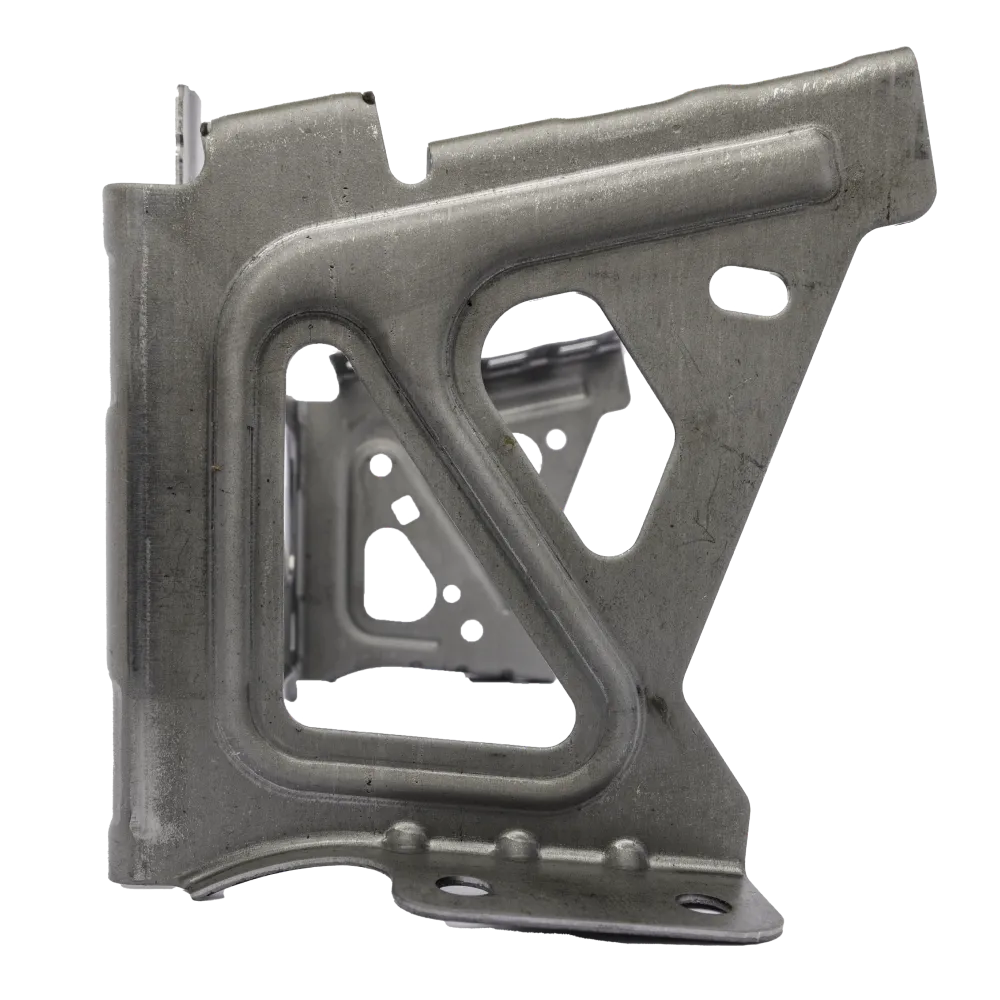
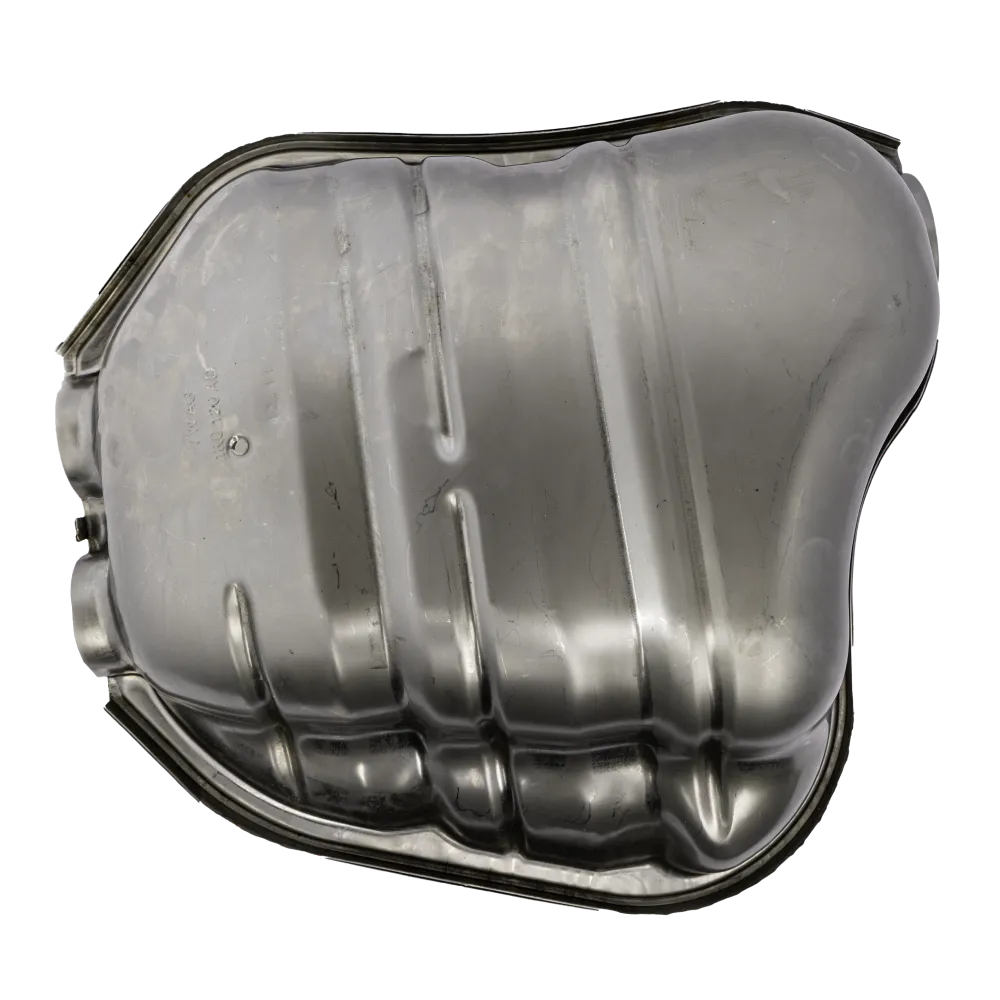
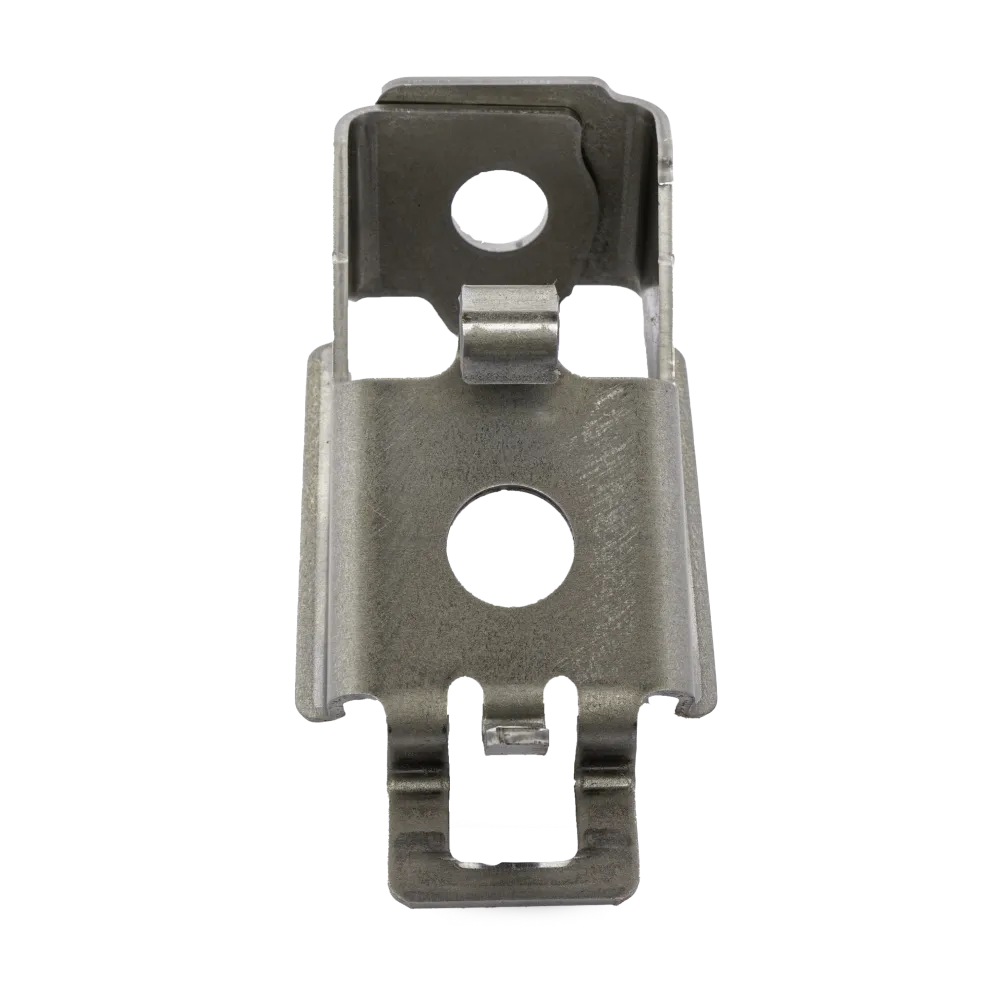
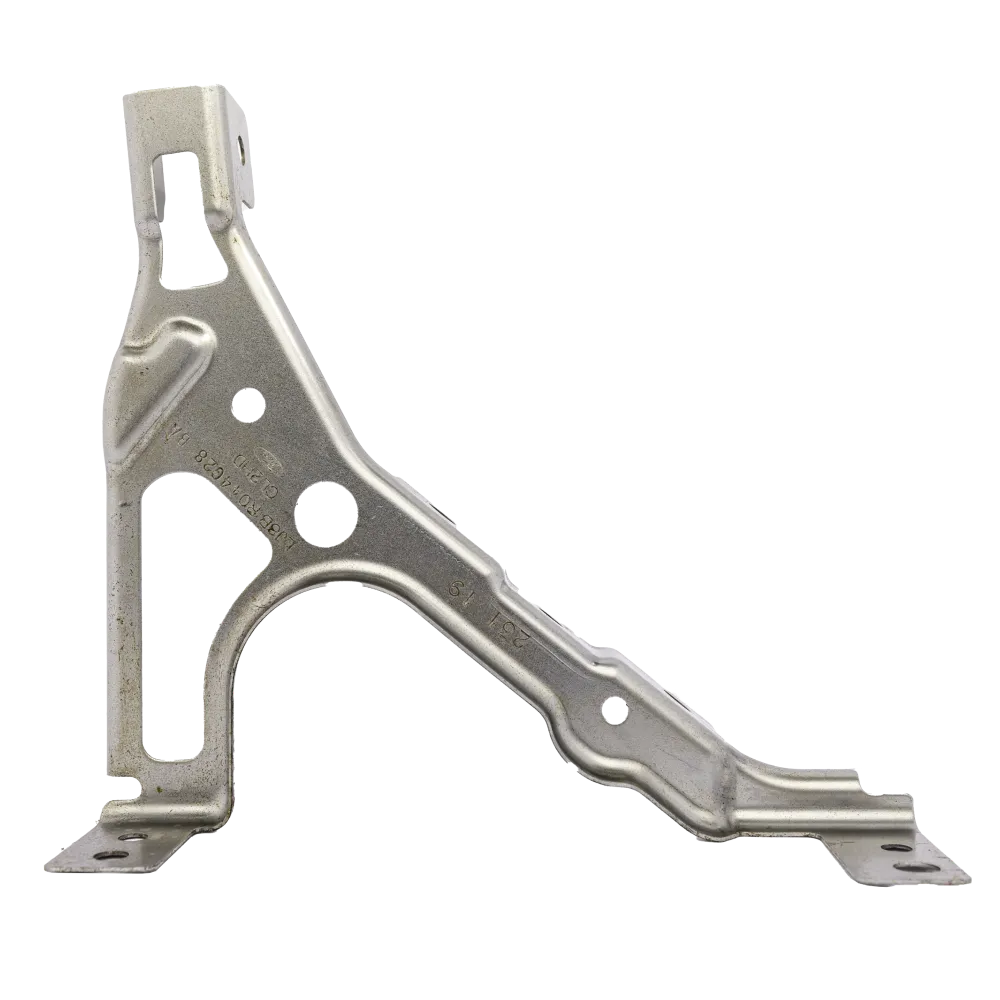
Every project is our best one yet.
Since 1979, we’ve focused on getting things right the first time so your tools run smoothly and efficiently at runoff and production. While our customers request key points of measurement, we require a 1.67 CPK or better for every point we measure.
Intentionally thoughtful from start to production.
We listen and learn on every project.
We’re persistent in our pursuit of a solution tailored to you, and we’re not afraid to ask questions and flex our approach along the way to create the best outcome.
No more games of telephone.
Our coordinated teams, combined with our robust ERP system help ensure coordination across project management, purchasing, machining, wire burn, CMM processes…well, really everything.
We keep our skills cutting-edge.
Our experience helps make us a leading partner to our customers. We excel at processing complex metals and crafting complete cells or lines.
Discover how we’ve helped our customers tackle challenges big and small.
We work with you headache-free.
We know that getting it right — up front — saves time, money, and hassle down the line. We’re committed to a transparent process that works for every project.
Riyaz Mohammed
Kirchhoff Automotive
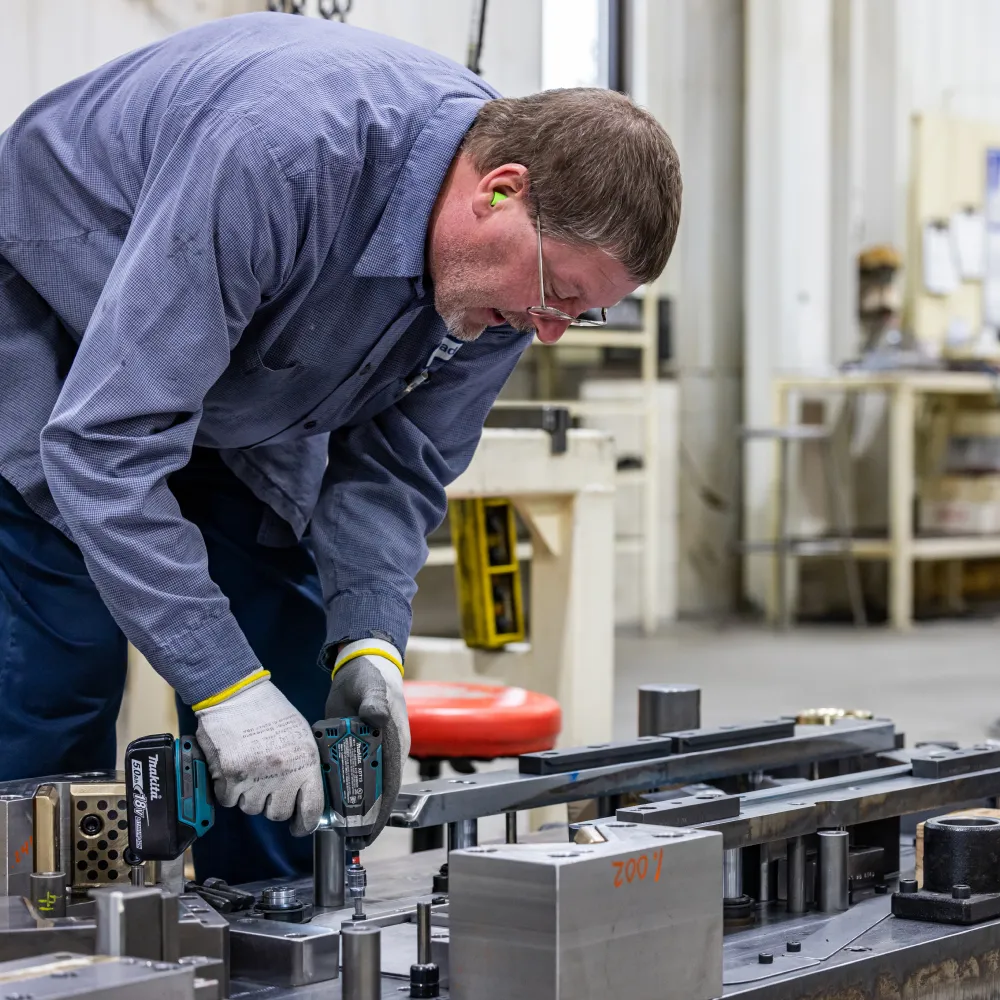
Quote and Kickoff
We gather requirements to concept and quote the project based on the information you provide.
We’ll kick off the project with all involved parties, sharing information to get everyone on the same page.
Design
Simulate, then design with regular reviews by both internal and external parties to ensure that the scope has been met.
Once approved, designs are released, then requirements added to the ERP system to ease ordering and scheduling. If outside resources are needed to ensure timing, our vast network of approved vendors are contacted to assist.
Periodic reviews with you provide a means to verify timing and scope are according to expectation.
Build and Verification
As materials are received, they are processed according to best practices in an organized and clean facility.
Assembly is performed by the appropriate team to ensure the best outcomes.
Equipment is verified through thorough measurement and dry cycling, then modifications are made until the product meets the set requirements.
CMM verifies quality of components processed according to customer and Pyper’s standards (1.67 CPK or better for all measured points).
Finalization and Deployment
You are welcomed to a final run-off of the equipment to verify that it meets the standard set forth.
Thorough documentation packages are created to provide the end user with as-built drawings and information pertaining to the operation, maintenance, and spare part requirements of the equipment.
Equipment is shipped to a specified location and installed if requested by the customer.
Support
Pyper answers the call for any final on site approvals and follow up as needed.
Don’t just take our word for it.
If you’ve dreamed it, we’ve probably done it. We leverage years of experience, a focus on continual improvement, and cutting edge technology to deliver quality every time. See what our customers have to say.
Randy Robeck
Ridgeview Industries
Dewayne Bain
Shiroki-NA
Brian Heykoop
Pridgeon & Clay
Tim Hickey
Shiroki-NA
Eric Cisneros
Kirchhoff Automotive
Riyaz Mohammed
Kirchhoff Automotive
You might be wondering…
We’ll keep this one short, but we’re always happy to show you. We’re different because of our vast knowledge base, our ability to be a one-stop-shop, and our flexibility to work with both simple and complex projects.
Actually the current Standard Lifters was a spin off from Pyper. We retain the ability to make many of these components in-house and work closely with Standard Lifters.
Our AIDA 3000 press can mimic your manufacturing conditions, minimizing setup time and duplicating real-world conditions as closely as possible. To verify quality we use a combination of Brown & Sharpe 9208 Coordinate Measuring Machine, 35” x 78” x 31½” and WLS Q-Flash with CT Mapping System. We measure all points to a CPK of 1.67 or better, not just the points that you ask us to measure.
Most die quotes can be turned around within 48 hours. Machine quotes are dependent on the size of the program and whether the quote is a budgetary or firm quote. We’ll let you know how long we estimate it will take.
There are always options to change processes, which may enable us to negotiate pricing. We always aim to give you a fair quote the first time.
There are always options to change processes, which could enable us to negotiate timing. We aim to give you a fair timing estimate the first time, while balancing our existing commitments. True timing won't be known until an order is received — we’ll do our best to estimate as we quote.
We can provide you with a list of affiliated companies who can provide check fixtures if you need them. We never recommend that the company building the equipment also build the check fixtures.
We can work through most terms, but it is dependent on project size. Our standard payment structure is to traunch the payment based on milestones at design approval, runoff, shipping, and install. We’ll talk about terms as you start discussing your project with us.
Projects require a purchase order and current release of CAD data to begin, however we can evaluate this on a case-by-case basis.
We have worked hard to be an efficient shop, but we’re also very flexible. We can switch the build floor daily if needed to accommodate a build, or test. When the time comes, we also have additional land for increased capacity on the same site.
We closely establish and monitor project timing and work with you to ensure program delivery is on time. Our ERP system allows us to reschedule based on live information as often as necessary. In the event that we determine our in-house capacity is a limiting factor, we also have established outside resources to assist us.
We’ll ask you questions as part of the quoting process, including your annual volumes, the maintenance and operating capabilities you have at your plant, and basic design requirements for the part. Refer also to our FAQ about the questions in the quoting process for a full list of the things we’ll ask you for.
We’re consultative and want to give you the best long-term result we can. We may review your design and suggest changes that may optimize manufacturing or potentially lower your cost.
When quoting on a machine, we will ask for:
-
Annual volume
-
Your established processes if you have them
-
Location where machine will be installed
-
Required lead time
-
Target pricing
-
Build specifications
-
CAD data
-
GD&T
When quoting on a die, we will ask for:
-
Press size that will run the tool
-
Die build specifications
-
Your established processes if you have them
-
Required lead time
-
Target pricing
-
Material type
-
CAD data
-
GD&T
We use AutoForm Simulation Software.
-
IGES
-
DXF
-
PARASOLID (Unigraphics)
-
STEP
-
CATIA
We’ll tell you the reason we decide to no quote, but most likely it’s due to timing or because we don’t feel we’re the best choice for that piece of equipment — but if we have a recommendation for who can help you best, we will share it.
If something does not function as quoted and approved once a piece of equipment is in the field, we will make it right. Our standard warranty is a year, however we pass along all manufactured part warranties. An extended warranty may be available, just ask for it.
At Pyper Tool, we pride ourselves on our commitment to quality. We hold ourselves to 1.67 CPK on all points we measure, not just the ones you specify—we’ve won industry awards because of our high standards. You can expect us to polish die steels even when we don’t need to—because we care about the details.
We love a good challenge! We have a track record of successfully delivering highly complex projects. Our customers choose us time and again and have relied on us to come through with proven solutions and novel approaches when required.
Our facilities are located in Grand Rapids. We have 43,000 square feet of air-conditioned shop space that we built to be efficient and modular.